How to Automate CNC Milling Machines
Horizontal Machine(s) + Automation = Rewarding Investment
This page explores the best practices for automating CNC milling machines. With the right machine tool strategy and automation capable of more than just moving pallets in numerical order, one can achieve the results of three machine tools with only one. To learn more, keep on reading or jump directly to our whitepaper using the link below:
Download our guide on automating CNC milling machines
Quick jump to:
1. Economical production of small batches
2. How to make one machine do the job of three?
Economical production of small batches
The vast majority of production in industrial machine building happens as make-to-order (MTO) manufacturing of batches – meaning in volumes everything from a single part to thousands of pieces per year. As there’s also variance in the workpiece mix, this kind of production is often called high-mix-low-volume (HMLV). Surprisingly many manufacturers are unaware of the huge potential flexible automation solutions offer in HMLV manufacturing and still operate manually. This page focuses on automating such production in the milling machine context.
The way to economical HMLV production is to remove the key barriers from the shop floor. When it comes to milling operations, these most often include unnecessary transfers, long set-up times, unstable quality, unit cost and tied capital, employee engagement and lead time pressure. Next let’s talk more about these six barriers – in case you want to go into the details of HMLV production and how to automate it, check out this page.
Unnecessary Transfers
Unnecessary transfers refer to all transports between manufacturing operations and storage that are not adding value to the product. The more transfers between operations, the more WIP and delays in production.
Long Setup Times
If setup changes between machined batches take a long time, it creates a natural temptation to produce larger batches than ordered, creating WIP and inventory. Furthermore, the production equipment might not be available for another, more urgent production order at the time of the over-sized batch production.
Unstable Quality
When quality is inconsistent and scrap rates high, manufacturers tend to produce extra work pieces, which again builds up unnecessary inventory.
Unit Cost and Tied Capital
When the processes are not reproducible, unit costs are dependent on production volume and the production is inflexible – again creating a need to produce more than what was ordered. Tied capital means basically inventories and work-in-process (WIP) that are a cause of too large batches.
Employee Engagement
One of the key challenges of today’s manufacturing is to find and retain skilled employees. The work is often physically consuming or even dangerous, work times varying depending on customer orders – and competition of skilled labor high.
Lead Time Pressure
All the previously mentioned barriers have a direct effect on lead times – lengthening them. At the same time customers are demanding for faster deliveries and more customized orders. In addition, non-reproducible processes make lead time estimations almost impossible.
To conclude, there are many painpoints in high-mix-low-volume production. How to overcome these barriers? In the next chapter we introduce three strategies on how to make more profits with milling.
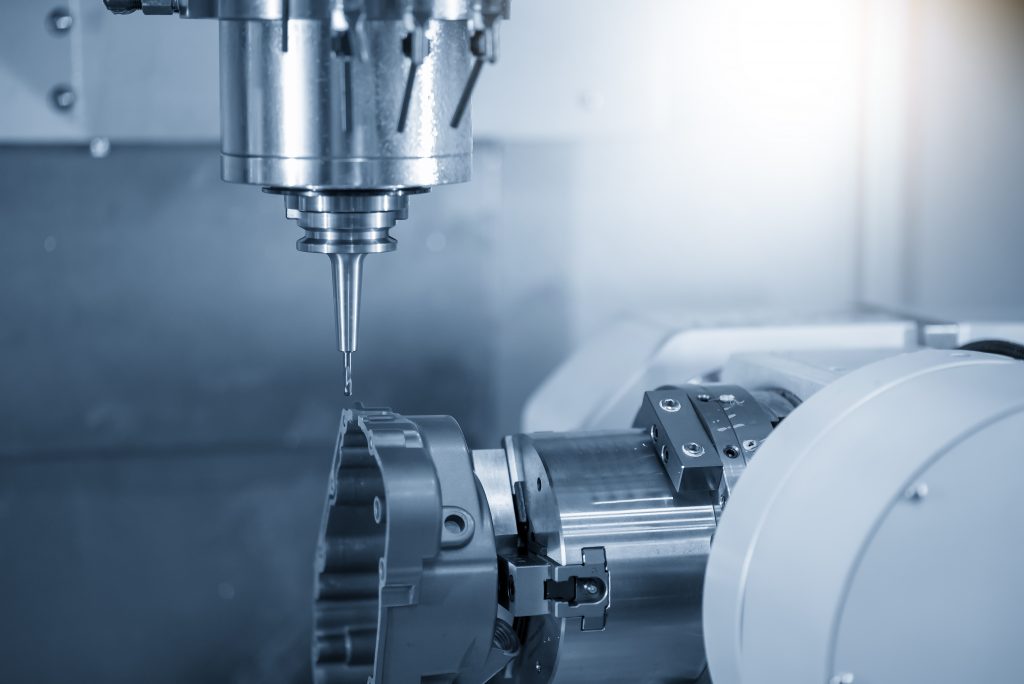
Investing in Multifunctional Machining Centers
Multifunctional, highly productive 4- or 5-axis machining centers have a lot higher of a price tag than traditional 3-axis machines. That said, one 4-axis machine with large enough tool magazine and the right automation can produce at the same rate as three 3-axis machines since this combination reduces the amount of machining operations. However, to justify the investment, the machine must be kept fed. These machines can withstand high workloads and feed rates for an extended period of time, which translates to following benefits:
- Increased production time
- Reduction of the setup times required for changing work pieces
- Reduction of overall waiting times
- Reduction of buffers while also maintaining service levels.
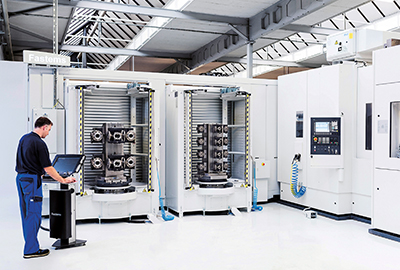
Automate CNC Milling Machines (and more)
After selecting suitable machine tool(s), it is time to look for a suitable automation solution. There are various different options for milling machines depending on the machine size, brand, amount of machines and the available space. The key idea in general is to minimize the amount of workpiece clampings and the production start setup times to maximize machine tool utilization. Things to consider when looking for the right automation solution:
- Machine tools: Is there one or more machines to be automated? Are there many machine tool brands that should be integrated with the same automation?
- Workholding: Are you using pallets, zero-point pallets or handling workpieces directly?
- Floor space: How much space is available for the system on the floor and vertically?
- ROI calculations: what option brings the greatest return in 1 year and in longer term?
- Future plans – should the system be extendable or modifiable?
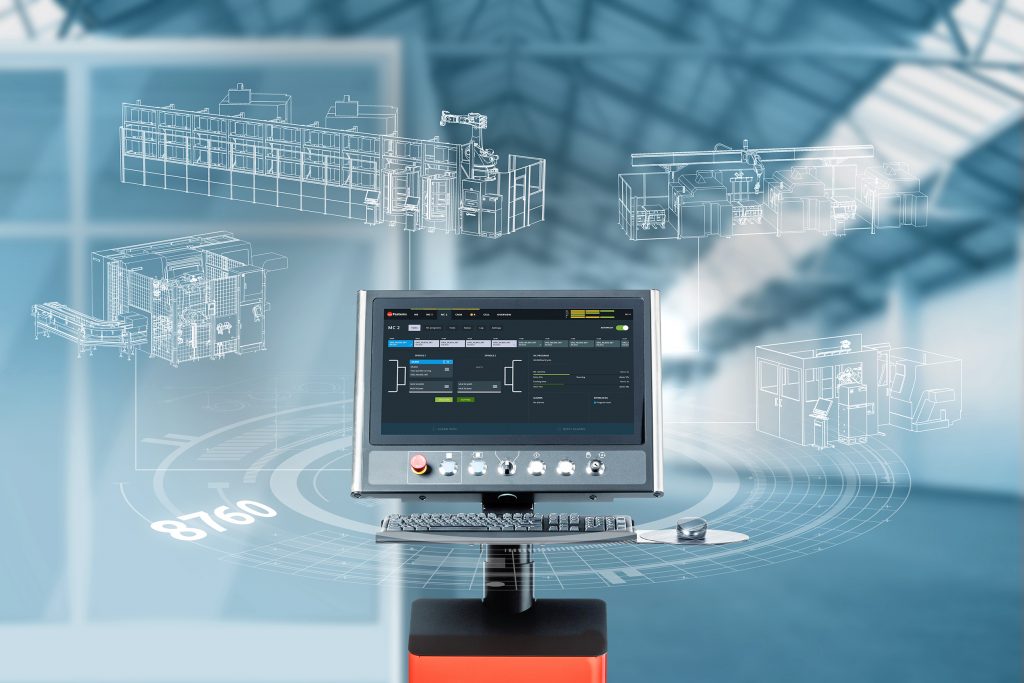
Automating also the Production Planning and Resource Management
In variable batch production physical automation – the replacement of operators with robots – isn’t enough alone. In addition, one needs efficient and automated production planning and production resource management. The main questions hinting us towards this direction are quite classical:
- How to deliver on time?
- How to adapt to sudden changes?
- How to avoid WIP and inventories?
- How to operate proactively, not reactively?
When faced with such questions, it quickly becomes clear that production can no longer be organized and planned with Excel spreadsheets, let alone with pen and paper. Instead, automatic production planning and production resource management should be considered. To learn what that means in practice, thake a look at Fastems’ Manufacturing Management Software (MMS)
Operational benefits
Lights-out production shifts, intelligent production planning including resource management, consistently high quality, more integrated processes and less waiting times are factors that result in operational excellence.
Happy employees and customers
With flexible automation the work of operators is safer and more meaningful. Constantly high quality with shorter lead times supply the customers with the right parts at the right time while keeping you profitable.
Financial benefits
Higher production capacity with lower labor and machine tool investment costs combined with decreased work-in-capital are all automation benefits.
Get Manufacturing Running with Queue Based Operation
The first step involves running production as a work-queue based operation per work station or machine. Instead of planning the production batch by batch, it will be scheduled for a longer period in a queue, helping operators to prepare for the coming batches in advance and extending the unmanned production times.
Utilize Simulation Based Work Queuing
With more automated approach the system can schedule production based on the end customer orders and available production resources, even when sudden changes occur. This is done by entering production data (NC programs, tools, fixturing, raw materials) into a master computer and making processes reproducible to cut down the setup times close to zero.
Pursue Data-driven Method Development
The third step is to start following production data and finetune production based on the findings. For instance: are some NC programs often slower than they should; are certain tools often breaking with specific workpieces; is the capacity utilized in a meaningful way? Data-based decisions leave no room for excuses or second-guessing.
Types of Pallet Automation
I know there are pallet pools, pallet towers and linear flexible manufacturing systems….But what solutions match my production? We’ve summed up the most critical factors for decision making to the table below.
Comparison | Pallet pool | Pallet tower | Linear pallet system |
---|---|---|---|
Pallet size | 400-1600mm | 320-630mm | 400-2000mm |
# of machine tools | 1 | 1 | 1-20 |
Unmanned production capacity per machine | 6 pallets | Up to 24 pallets | Unlimited |
Avg machine utilization | 65 % | 80 % | 85 % |
Machines run per operator | 1 | 1 | 3 |
Extendability | Buy a new system | Buy a new system | Easy extension |
Automatic production planning | No | Yes* | Yes* |
Order priorization | Manual | Automatic* | Automatic* |
Automatic real-time KPI reports | No | Yes* | Yes* |
* Depends on automation control software. For example, Fastems MMS includes this feature.
Or rather talk or mail directly with us?
"*" indicates required fields