Une automatisation tout-en-un, changement de configuration compris – Une cellule robotisée agile pour la manipulation des pièces et des palettes
Il s’agissait probablement de l’un des projets d’automatisation les plus ambitieux à ce jour d’ALLMATIC – Jakob Spannsysteme, quelque chose d’inédit et d’unique, à savoir la création d’une cellule robotisée servant à la manipulation de palettes et de pièces à usiner. L’un des aspects les plus difficiles était de répondre au souhait d’automatiser le changement de configuration d’une machine, et ce afin d’assurer la production 24 heures sur 24.
ALLMATIC – Jakob Spannsysteme GmbH développe et fabrique des étaux pour machines, qui peuvent prendre la forme d’étaux haute pression pour les fraiseuses conventionnelles mais aussi de solutions complexes garantissant la flexibilité des centres de production. L’entreprise propose en outre des solutions adaptées à des besoins particuliers. Pour son Directeur des opérations, Herbert Mayr, ALLMATIC – Jakob Spannsysteme compte parmi les principaux fournisseurs de son domaine d’activité. Toutefois, l’entreprise n’a pas pour objectif de vendre plus d’étaux que ses concurrents pour devenir le leader du marché.
M. Mayr précise : « Nous nous efforçons plutôt de devenir le leader technologique dans notre secteur d’ici 2030. Dans l’intérêt de nos clients, nous devons continuellement développer des produits innovants, travailler à des solutions plus intelligentes et, surtout, mettre plus particulièrement l’accent sur l’automatisation. À cet égard, l’un de nos projets les plus ambitieux a été le développement et la réalisation d’une cellule robotisée qui est automatisée pour fabriquer jusqu’à 32 composants différents pour des étaux en lots individuels de plus de 100 unités par ordre de fabrication, 24 heures sur 24. Cela permet de combiner non seulement la manipulation des palettes et des pièces à usiner au sein d’un seul système, mais aussi d’assurer le changement de configuration de la machine sans surveillance. »
« Face à de telles aspirations, de nombreux directeurs d’exploitation d’autres fabricants de machines se contentent au départ de secouer la tête », explique M. Mayr, qui ajoute : « C’est ainsi que j’ai rencontré le directeur des ventes de Fastems, Thomas Weinhold, lors d’une exposition interne de la Gebr. Heller Maschinenfabrik. Ses questions très précises m’ont fait réaliser que j’avais rencontré quelqu’un qui comprenait vraiment ce que je prévoyais. Pour faire court : grâce Fastems et Heller en tant que fournisseur de machines et entrepreneur général pour le projet, nous avons pu mettre en œuvre l’idée d’une cellule robotisée. »
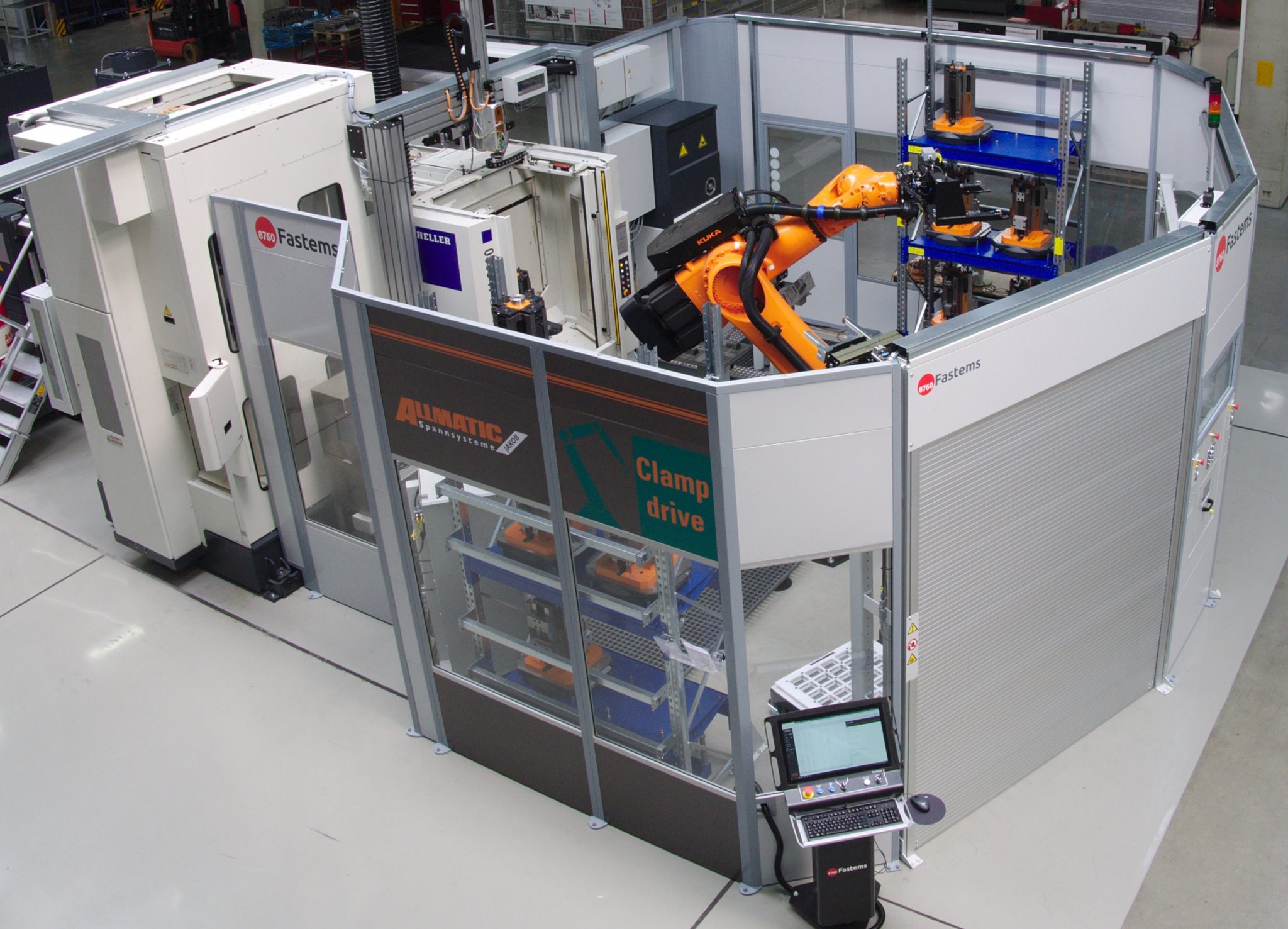
Cette cellule robotisée, qu’ALLMATIC utilise depuis 2018, est unique et présente plusieurs caractéristiques particulières.
Un démarrage de la production par code à barres
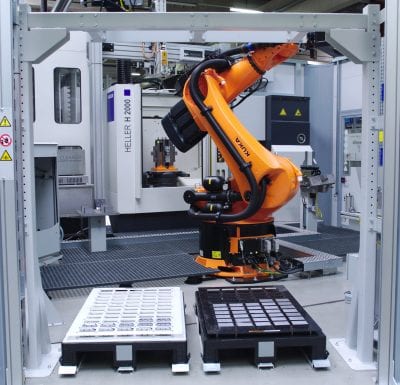
Une des deux stations matière première, chacune conçue pour 2 palettes Europe en plastique pour les pièces brutes et finies.
Les différents composants de la cellule robotisée (voir encadré : une cellule robotisée agile) et, notamment la description du processus de production type, nous éclairent sur ce qui rend cette solution d’automatisation si particulière.
Luis Paiba, responsable du développement et de la conception chez ALLMATIC, explique : « Des deux côtés des stations matière première se trouvent 2 palettes, chacune servant aux matières premières et aux pièces finies, de sorte qu’il est possible de réaliser, et ce sans surveillance, jusqu’à 2 commandes différentes, y compris des changements de configuration de machines entièrement automatisés. »
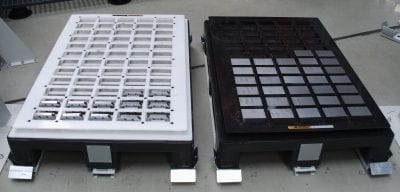
Les moules ALLMATIC pour palettes de matières premières et de pièces finies sont conçus de manière optimale pour être manipulés par des robots.
Lorsqu’un ordre de fabrication arrive, le robot commence par scanner le code barre de la matrice de la matière première et reçoit ainsi tous les détails du processus de production en cours. À cette fin, le logiciel de gestion de la fabrication (MMS) de Fastems met automatiquement en œuvre les programmes appropriés pour l’automatisation et l’usinage de la pièce. Grâce à une pince à aimant permanent, le robot récupère une pièce brute de la matrice et la transfert sur un support de préhension pour la positionner avec précision. Ensuite, le robot achemine la pièce à usiner jusqu’à la station de prélèvement, puis charge la palette de la machine à l’aide de la pince parallèle.
Un usinage complet avec 2 procédures de bridage
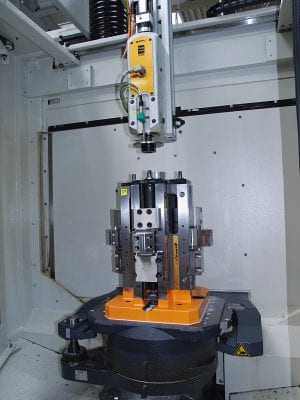
Le système ALLMATIC Clamp Drive (ci-dessus) permet de monter les pièces sans intervention humaine.
Les processus de fabrication courants comptent toujours 2 montages d’usinage sur la machine, de sorte que la production peut être continue et qu’un usinage sur 6 axes est alors possible en seulement 2 étapes de processus (OP10 et OP20). Le bridage automatisé et flexible des pièces est assuré par le système ALLMATIC Clamp Drive, qui est monté sur le côté robot du changeur de palettes de la machine.
Un ordre de production commence toujours par une palette vide ; les pièces sont serrées sur le premier montage d’usinage (OP10), tandis que l’OP20 reste vide pendant la phase d’usinage. Une fois le processus d’usinage terminé, les pièces à moitié prêtes sont temporairement stockées devant la machine, puis bloquées sur le deuxième montage d’usinage (OP20). Après le changement de palette, le robot peut commencer à charger le premier dispositif (OP10) avec de nouvelles pièces brutes. La rotation continue des étapes des processus de OP10 et OP20 permet ensuite d’assurer le traitement de l’ensemble de l’ordre. Si un composant vient à changer, le robot achemine la nouvelle pièce nécessaire vers la machine, tandis que les dernières pièces installées restent dans la machine.
Une fois le processus de fabrication complet terminé, le robot change automatiquement, si nécessaire, les palettes requises pour les nouvelles pièces à usiner grâce à des dispositifs situés à l’intérieur de la machine.
Un potentiel d’optimisation des processus
« Avec une solution d’automatisation aussi complexe que celle-ci, nous devons encore acquérir beaucoup d’expérience pour pouvoir identifier les potentiels d’optimisation possibles des différents processus », souligne Herbert Mayr.
Actuellement, le robot débarrasse toutes les pièces semi-finies et les place sur la station tampon, avant de charger ces mêmes pièces sur le montage d’usinage OP20. Pour pouvoir enlever toutes les pièces, la palette doit être retournée. Un processus de bridage parfaitement sûr nécessiterait toutefois de référencer Clamp Drive entre les brides, ce qui coûterait un temps précieux. « C’est ce que nous voulons changer en demandant au robot d’enlever d’abord une pièce à moitié prête, puis de charger immédiatement une nouvelle pièce brute à la même position du bridage, sans avoir à tourner la palette », explique M. Mayr.
La programmation paramétrique minimise
les périodes de temps non productives
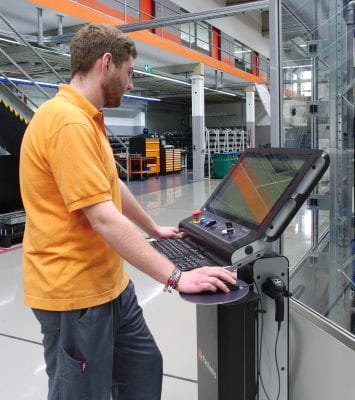
Voici l’employé responsable du système ALLMATIC, situé à côté du terminal servant au MMS de Fastems, qui s’occupera entre autres de l’ensemble de la planification, du contrôle et de la surveillance du processus de fabrication automatisé. En plus de cela, il assurera certes la gestion des programmes CN, mais gérera également les 160 outils et surveillera leurs périodes d’immobilisation.
Du fait que la cellule agile de fabrication de ALLMATIC est conçue pour des processus de production sans surveillance sur de longues périodes, l’introduction de nouvelles pièces, y compris l’adaptation de la cinématique du robot, ne devrait durer que le minimum de temps possible. La programmation paramétrique du robot via le logiciel de gestion de la fabrication (MMS) apporte un soutien essentiel pour y parvenir.
« Des connaissances particulières sur les robots ne sont pas nécessaires », explique Luis Paiba qui poursuit : « Fastems avait déjà mis à notre disposition quelques programmes pour la fabrication des pièces à usiner à l’avance. Chaque fois qu’une nouvelle pièce doit être fabriquée, les séquences d’acheminement nécessaires peuvent être facilement ajustées en entrant des paramètres spécifiques (étapes de manipulation), sans perdre de temps à programmer le robot. Nos employés ont déjà utilisé cette méthode pour créer 17 nouvelles séquences de déplacement pour le robot. »
Luis Paiba, Responsable du développement et de la conception chez ALLMATIC, précise :
« Si nous souhaitons devenir le leader technologique, nous devrons également nous occuper de l’automatisation de manière plus consciente, et pas seulement dans le seul intérêt de nos produits. »
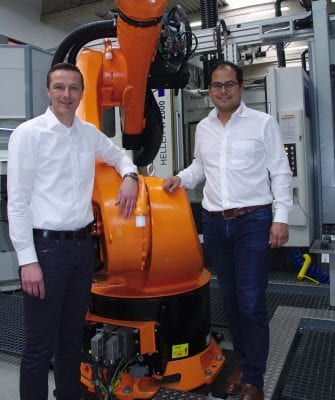
Herbert Mayr (à gauche), Directeur des opérations, et Luis Paiba, Responsable du développement et de la conception, ont acquis de précieuses connaissances au cours du projet.
Repenser et apporter de précieuses informations
Grâce à ce système automatisé, ALLMATIC a pu non seulement obtenir des résultats probant en termes de productivité et de flexibilité dans son processus de fabrication, mais, pour Luis Paiba et Herbert Mayr, l’entreprise a également acquis de précieuses connaissances.
« Toutes les pièces qui sont désormais produites avec la cellule robotisée étaient déjà fabriquées par nos soins. En raison de l’automatisation, nous avons dû envisager les choses de manière différente et avons ainsi pu identifier de nouveaux potentiels pour optimiser nos processus et procédures. Par exemple, les pièces peuvent maintenant être entièrement usinées en deux étapes de bridage au lieu de trois. Nous avons adapté nos pièces dans ce but. Nous avons également automatisé des processus de travail autrefois manuels en intégrant un poste de soufflage et d’application antirouille à la cellule », explique Luis Paiba.
Herbert Mayr, Directeur des opérations chez ALLMATIC, explique :
« De nombreux fabricants étaient septiques à l’évocation de mon idée de passage à l’automatisation. Mais avec Fastems, nous avons maîtrisé ce défi et bien d’autres encore. »
Ce n’est pas seulement une victoire en termes de capacité
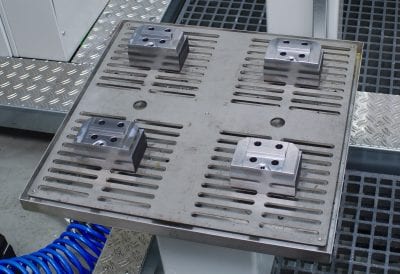
Voici la station de prélèvement de pièces préalablement usinées. Actuellement, la cellule robotisée permet de produire 32 pièces à usiner différentes utilisées par les étaux de machines, en lots de plus de 100 par ordre de fabrication, p. ex. des mâchoires, des éléments de base ou des plaques de pression et de serrage.
Et Herbert Mayr a acquis une autre connaissance cruciale :
« L’automatisation sécurise les emplois, car nous pouvons désormais réagir bien mieux aux fluctuations des commandes. À l’heure actuelle, notre cellule robotisée fonctionne à 90 % de sa capacité, produisant 32 composants différents sans intervention humaine, par un roulement de deux équipes « fantômes ». Si le nombre de commandes entrantes devait fortement diminuer, nous ne serions pas automatiquement contraints de supprimer des emplois puisque la cellule robotisée pourrait fonctionner avec un seul poste sans surveillance. »
Une cellule robotisée agile : ses principales propriétés
-
L’utilisation du dispositif Heller H 2000 et d’un magasin comptant actuellement 160 outils (pour une capacité totale de 409 outils) permet un usinage complet sur la base de 2 procédés de bridage. Cette photo montre une palette de machine dans l’espace de travail du BAZ à 4 axes. Une autre palette est placée à côté de cette installation, ce qui permet d’échanger les palettes à tout moment.
Une des deux stations matière première, chacune conçue pour 2 palettes Europe en plastique (pour les pièces brutes et finies)
- Étagères de stockage pour 12 palettes de machines avec dispositif de serrage ALLMATIC
- ALLMATIC Clamp Drive servant au serrage et au desserrage des pièces à usiner
- Centre d’usinage 4 axes Heller H 2000 pour l’usinage des pièces sur 6 axes
- Robot Kuka KR600 (capacité de manutention de 400 kg max.)
- Pince à palette et double pince de Schunk pour la manutention des pièces à usiner (pince à aimant permanent / pince parallèle)
- Poste de traitement antirouille
- Poste de soufflage
- Station de chargement de préhension / support tampon
- Tiroir pour mesurer les pièces à usiner
- Lecteur de code à barres
- Manufacturing Management Software (MMS)
pour la gestion automatisée de la production
Spécialiste des systèmes de serrage
ALLMATIC a été fondée en 1973 et est devenue l’un des principaux fournisseurs de systèmes de serrage depuis 2001, date à laquelle elle est devenue membre du groupe Jakob. Elle fabrique des produits tels que des broches filetées mécaniques simples, des étaux à commande numérique (c’est-à-dire équipés d’amplificateurs de puissance) et des étaux « Gripp », par exemple pour un usinage sur 5 axes, ainsi que des solutions de serrage multiples et spécialisées.
Comptant actuellement 73 employés, dont 16 apprentis, l’entreprise développe et fabrique des solutions innovantes pour le marché international depuis son siège d’Unterthingau, dans l’Allgäu, en Allemagne. Son principal marché est l’Europe, et en premier lieu l’Allemagne, suivie de l’Autriche, l’Italie, la France et la Roumanie. En 2018, ALLMATIC – Jakob Spannsysteme a réalisé un chiffre d’affaires d’environ 10,8 millions d’euros.
Article initialement publié dans « NC Fertigung », édition 07-08/2019
Voir Clamp Drive en action
Related products:
"*" indicates required fields