La perfection en pratique
Une stratégie « zéro erreur » et un haut degré d’automatisation ont permis de réduire la durée de changement des outils
Lorsque des problèmes et des erreurs d’usinage qui auraient pu être tolérés autrefois atteignent un certain seuil, il est temps de penser à apporter des modifications. Et c’est précisément ce qu’a fait l’entrepreneur Stefan Kempf. Le résultat se décline sous la forme d’un système de fabrication hautement automatisé et extrêmement flexible, qui est probablement unique en son genre dans le pays.
Avec un effectif de 100 personnes, l’entreprise Norbert Kempf CNC-Technik GmbH sise à St. Ingbert (dans la Sarre, en Allemagne) fabrique des composants simples à très complexes en lots de 1 à 500, ainsi que des prototypes pour des applications pneumatiques et hydrauliques, destinés à l’industrie automobile et aux machines de construction. Fondée en 1970 par Norbert Kempf sous la forme d’un simple atelier de tournage, l’entreprise n’a cessé de croître. Lorsque Stefan Kempf rejoint l’entreprise de son père en 1990, la société commence à s’orienter vers la production CNC. Neuf ans plus tard, l’entreprise compte plus de dix centres d’usinage CNC.
La croissance conventionnelle a ses limites
« Nous nous sommes alors rendu compte que la croissance classique passant par le seul achat de machines avait ses limites. En fait, plus nous installions de machines, plus notre productivité déclinait. Le personnel qualifié, dont il fallait disposer à l’époque pour changer les outils, était difficile à trouver et notre organisation et ses processus de soutien environnants devenaient de plus en plus difficiles à gérer pour nous. Ces processus étaient tout simplement instables », explique Stefan Kempf, Directeur général. Nous avons ainsi commis de plus en plus d’erreurs, ce qui nous a coûté beaucoup de temps, de patience et d’argent pour y remédier. Mais cela ne pouvait pas continuer ainsi.
« J’étais fatigué d’arriver au travail tous les matins et d’être toujours confronté aux mêmes problèmes, erreurs et situations. C’est pourquoi j’ai décidé de procéder à un changement radical », explique M. Kempf, en décrivant la situation de la production CNC « traditionnelle » alors en vigueur. « À cette époque, nous comptions environ cinq changements d’outils par jour, 250 acheminements manuels pour l’outillage, 40 à 50 acheminements d’outils dus à l’usure et ce, pour une moyenne de six assemblages de pinces. Toutes ces activités présentaient un fort potentiel d’erreurs, et la gestion des outils en particulier s’est avérée être une source majeure de problèmes. »
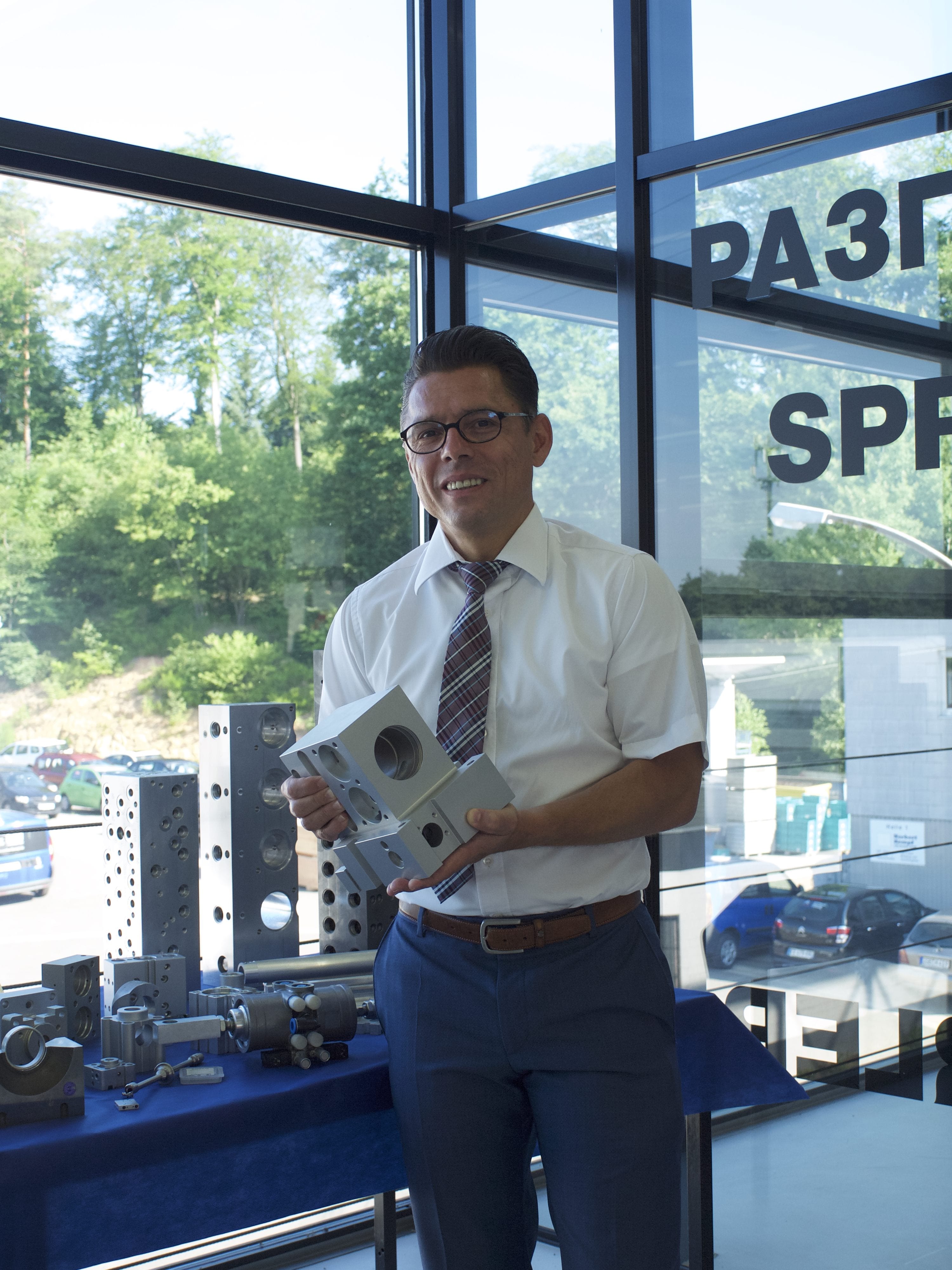
Stefan Kempf, PDG
La technologie FMS se développe progressivement
La question était de savoir comment effectuer ces tâches sans commettre d’erreurs, et ce, au plus près du temps d’usinage. La réponse se trouvait dans une automatisation maximale. Mais avant cela, il fallait s’assurer de préparer les processus commerciaux les plus importants. Stefan Kempf : « Nous avons commencé par acheter un système de gestion de données d’outils et avons investi beaucoup de temps dans la mise en place d’un système de gestion véritablement complet. En parallèle, nous nous sommes assurés de pouvoir fabriquer nous-mêmes les palettes d’usinage et les dispositifs de serrage des pièces à usiner. C’est seulement à ce moment là que nous avons décidé d’installer un système de fabrication flexible assorti du système multi-niveaux (MLS) de Fastems ».
En 2003, une machine existante avait été reliée au système MLS (avec une capacité de 12 palettes d’usinage). En 2011, le système s’est progressivement développé pour atteindre la configuration maximale possible avec un total de quatre stations de chargement et 96 palettes d’usinage sur trois niveaux. En plus de la machine existante, cinq autres centres d’usinage Mori Seiki NH 4000 ont été reliés au système MLS. « Dès le début, nous avons veillé à ce que les interfaces d’outils et les palettes d’usinage de ces machines soient standardisées, chaque machine disposant d’une grande capacité de stockage d’outils capable d’accueillir 180 emplacements d’outils. »
Les outils comme facteur contraignant
Bien que le système FMS ait apporté à l’entreprise un gain de productivité important, Stefan Kempf considérait que le système présentait un inconvénient majeur : « Étant donné que notre gamme de fabrication comportait des lots pouvant varier de 1 à 500, et environ 18 000 références de pièces dans notre portefeuille, le nombre d’outils sur les machines n’était pas suffisant pour effectuer toutes les opérations de production, qui étaient essentiellement dictées par les 96 palettes du système, présentes sur chacune des machines. Cela signifiait que nous devions toujours allouer un certain nombre de palettes à une machine donnée. » Il était donc impossible de maintenir un niveau élevé d’utilisation des machines. M. Kempf explique par ailleurs qu’un certain nombre de sources d’erreur continuaient à empêcher une production vraiment fiable.
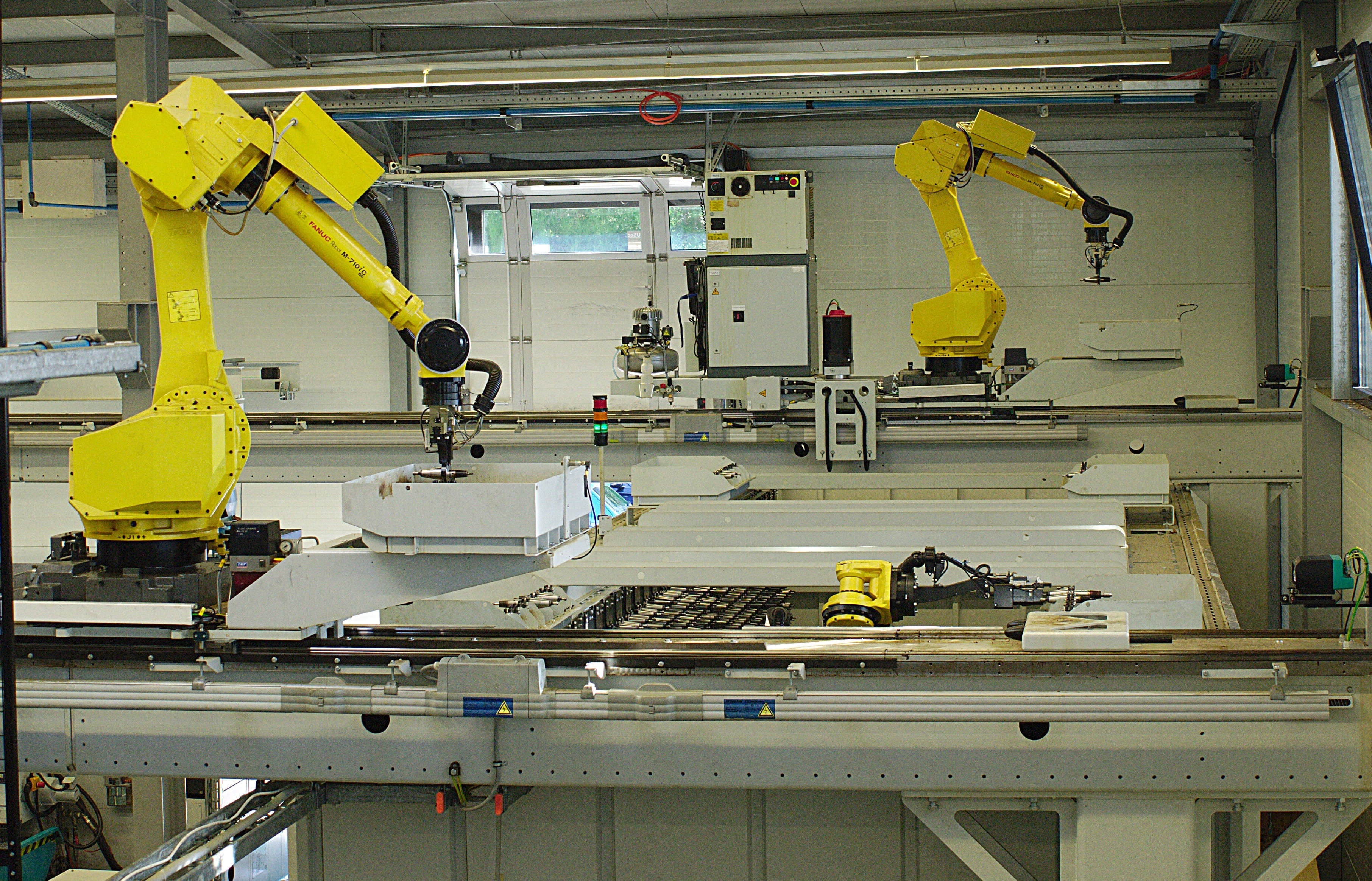
Un stockage centralisé, deux lignes de production, trois robots : un robot du CTS de Fastems (au centre) transfère les outils aux deux robots sur structure métallique. Au premier plan se trouve le robot qui alimente les machines du système MLS. À l’arrière-plan, un autre robot transfère les outils vers cinq autres centres d’usinage.
Un stockage centralisé pouvant accueillir 2 500 outils
C’est pour cette raison que la société a, en 2013, investi dans un autre FMS de Fastems comprenant un magasin de matières premières, incluant par ailleurs la construction d’un nouveau hall. Avec une charge utile de 1 000 kilogrammes par palette, le MLS-MD (charges moyennes) propose un espace sur quatre niveaux totalisant 156 palettes, dont la moitié sont des palettes d’usinage et l’autre moitié des palettes de matières premières. Le système, qui est désormais relié à sept centres d’usinage, dispose de quatre cellules de chargement, chacune d’entre elles s’accompagnant d’une station de chargement pour la palette d’usinage et d’une station pour la palette de matières premières. En parallèle, les cinq autres centres d’usinage sont automatiquement approvisionnés en outils depuis le magasin d’outils centralisé.
Ce système est d’autant plus remarquable qu’il combine le magasin centralisé d’outils Fastems CTS, qui contient 2 500 outils, et un robot assurant le transport de ces derniers. Comme chaque machine possède également son propre magasin contenant 60 outils, le système donne accès à 3 200 outils. Et cela à partir de chaque machine, car une structure métallique équipée du robot permet d’acheminer les outils depuis le stockage centralisé au centre d’usinage correspondant, en fonction des besoins. Pour permettre au lecteur du robot d’identifier un outil individuellement, chaque outil préréglé est équipé d’une puce RFID.
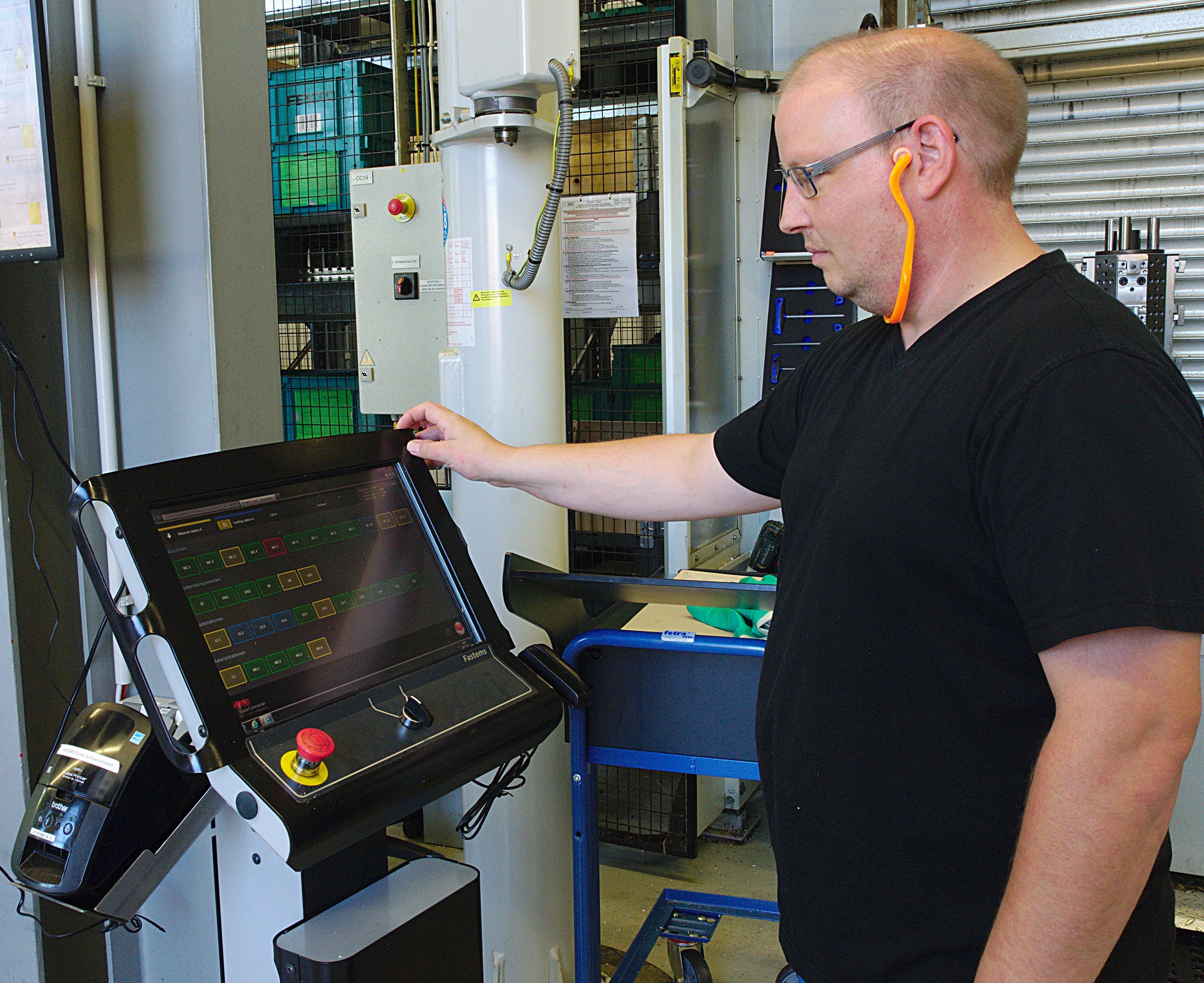
Chacune des cellules de chargement dispose d’un terminal sur lequel le MMS de Fastems est installé. Le logiciel contrôle des éléments tels que l’ordre des palettes en fonction des tâches dans le MLS et gère tous les programmes CNC et les données relatives aux outils.
Le logiciel gère la planification et le contrôle de la production
En tant que principal système intelligent, le logiciel de gestion de la fabrication (MMS) de Fastems gère l’ensemble des tâches liées à la planification et au contrôle de la production dans le FMS. Cela inclut l’acheminement des outils assisté par un robot, et ce, depuis le stockage centralisé des outils (CTS) jusqu’aux machines. Cependant, le logiciel ne se contente pas de contrôler la logistique des livraisons, dans laquelle il planifie l’ordre des palettes dans le système, mais il gère également tous les programmes CNC et les données des outils. Avant que la production ne commence, le MMS effectue également un contrôle des ressources pour vérifier, entre autres, si la matière première nécessaire est présente dans le système et si les outils requis pour un ordre de fabrication spécifique ont la durée de vie nécessaire. « Si la durée de vie d’un outil n’est plus suffisante pour l’usinage, notre système de montage et de préréglage des outils reçoit automatiquement un message du logiciel », explique Stefan Kempf, qui souligne par ailleurs : « Un point important pour nous, avant même la mise en service du FMS, était de garantir les préparatifs de la production essentiels à la fiabilité des processus de production. C’est pourquoi nous lançons un ordre de planification de processus pour chaque nouvelle pièce ou chaque composant modifié. De l’analyse AMDE, au plan de contrôle de la production, en passant par la conception des outils et la programmation CNC, chaque étape est planifiée à l’avance, en mettant toujours l’accent sur la fiabilité du processus. »
Un changement des outils entièrement automatisé
Grâce à la toute dernière version du FMS, l’entreprise est désormais en mesure d’effectuer chacune des opérations de traitement de chacune de ses machines, ce qui permet d’automatiser complètement le renouvellement des outils. « La durée de renouvellement des outils est en fait de 0,0 minute, ce qui signifie qu’un composant a toujours le même prix pour nos clients, qu’ils en commandent dix ou cent », explique Stefan Kempf, soulignant un avantage clé de sa fabrication hautement automatisée et flexible, alors que d’autres chiffres impressionnants parlent déjà d’eux-mêmes : environ 1 000 acheminements d’outils et 500 acheminements de palettes ont lieu chaque jour dans le système. L’utilisation moyenne des broches de l’ensemble des machines se situe entre 95 % et 98 %.
Pousser l’automatisation à ses limites
« Malgré ces niveaux élevés d’automatisation, nous n’avons pas réduit nos effectifs depuis l’installation du FMS, mais avons atteint une croissance annuelle moyenne de 15 % depuis 2014 tout en conservant le même nombre de salariés », explique M. Kempf. Ce dernier pourrait se contenter de ce qui a déjà été réalisé, mais il en veut plus : « La flexibilité que nous gagnons en pouvant traiter chaque pièce sur chaque machine du FMS est si grande que nous voulons poursuivre cette approche. » Un nouveau hall de production est actuellement en construction. Un autre MLS de Fastems y sera installé, et sept centres d’usinage horizontaux seront connectés à ce qui est désormais le troisième FMS. De l’autre côté des halls, un robot sur structure métallique accédera au stockage des outils du deuxième FMS et au nouveau système. « Nous allons utiliser le GTS (stockage d’outils sur structure métallique) de Fastems pour accueillir des emplacements d’outils supplémentaires dans le nouveau FMS afin de gagner de la place dans la zone de production. Le robot de ce système effectue deux tâches. « Il achemine les outils entre le hall 3 et le nouveau bâtiment et peut également alimenter les nouvelles machines en outils », explique Stefan Kempf en évoquant la planification.
Publié dans « Automationspraxis », numéro 09/2017
Related products:
"*" indicates required fields